黄石东贝:助推“四省”,智造升级加速定制化进程
本文由 电器杂志 发表,转载请注明来源!
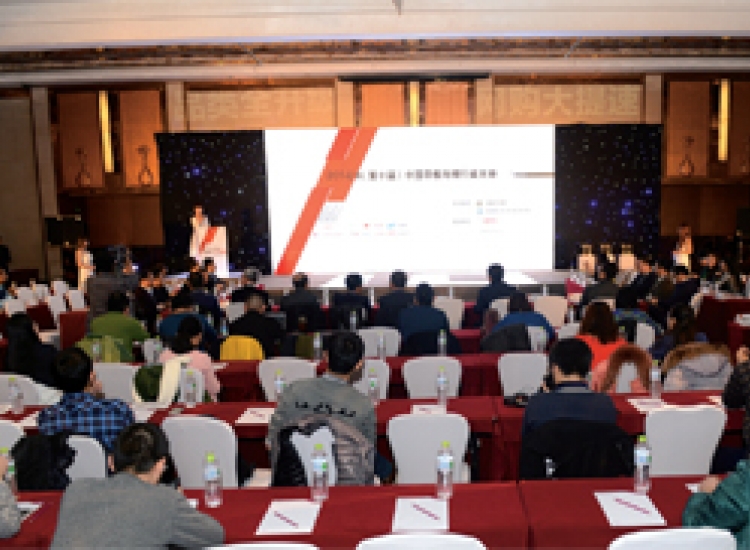
智能制造已成为制造业发展的必然趋势。智能制造升级既符合中国制造业从“制造大国”向“制造强国”的转型要求,也能提质增效,节约社会资源并降低成本,同时还能满足日益提升的定制化市场需求。11月17日,在“寻找中国家电业智能制造先锋大型主题活动”期间,《电器》记者来到黄石东贝电器股份有限公司(以下简称黄石东贝),通过采访以及对“最前线”的实地参观后发现,黄石东贝正在描绘一幅高效灵活的生产模式、产业链有效协作与整合、新型生产服务型制造、协同开发和云制造的智能制造蓝图。
“四省”
关于智能制造升级对制造环节的提升,黄石东贝电器股份有限公司工程部部长尤琼兵用了“四省”来总结。所谓“四省”,分别为省人、省力、省耗以及省心。他进一步解释说:“省人,是指精益智能化可以相对减少用工;省力,是指针对劳动强度比较大的岗位,通过智能化改造,减少人的劳动强度;省耗,是指智能制造升级可以减少能源消耗,降低制造成本;省心,是指以前很多需要人工收集的质量和检测数据在智能化升级后可以由系统自行采集和反馈,并全流程跟踪质量情况。”
《电器》记者在参观黄石东贝标杆生产线时,对这“四省”有了深刻地感受。在省人方面,记者粗略地数了一下,整条生产线的员工不足40人。据黄石东贝电器股份有限公司副总经理朱宇杉介绍,改造前该生产线需要80位员工。令《电器》记者印象深刻的是,对产品质量影响较大的焊接工序,黄石东贝已经实现自动化升级,通过机器人来节省人力,5台焊接设备仅需要1位工人操作管理即可。尤琼兵提供的黄石东贝三大基地2014~2017年人数曲线图呈明显下降趋势,也可以印证智能制造升级对人员减少的影响。该数据显示,截至2017年10月,黄石东贝三大基地人数较2015年减少1268人。
朱宇杉进一步介绍道:“以前仅跑合线这一道工序就需要十几人,智能化升级后,现在5个工人就足够了。这对效益和效率都有提升。但也产生了一个问题:对设备维修人员的技术水平要求提高了。人才储备变得更为重要。”
在参观过程中,整条生产线并未见到需要人工搬运等劳动强度大的工序。黄石东贝机电集团有限责任公司总裁朱金明指出,越来越多的“90后”“95后”开始进入工厂,他们对工作环境要求更高。“而且,黄石东贝所在的地理位置并不利于招工。因此,对于劳动强度较大的岗位,我们会优先考虑设备自动化升级。”
产品质量和生产效率提高
黄石东贝智能制造升级后,另外一大特点就是质量管控得到提升,产品质量的稳定性提高。参观变频压缩机标杆生产线时,朱宇杉告诉《电器》记者,这条生产线经过对设计、供应、质量和过程控制四方面的提升,生产出的产品可以做到10年质保。“在智能制造升级后,我们产品设计的可靠性得到提高;在供应链方面,可以通过系统对比各项数据选择优质的供应商,保证零件的可靠性;在质量和过程控制方面,不仅通过质量管理控制,还通过对员工定员定岗来控制。”
信息化时代,数据变得非常重要。朱金明表示:“过去,生产时的质量数据都靠人工收集,不仅复杂,而且容易造成误差,致使数据分析出的结果不够准确。信息化后,生产时的重要数据都可以由系统自动采集,数据实时且准确,分析出的结果对产品设计及质量稳定性也更有帮助。”
朱宇杉指出,经过智能制造升级后,产品质量和可靠性都得到很大提升,标杆生产线不合格产品下线率也因此下降为50ppm~100ppm。据尤琼兵介绍,宿迁基地新建中的数字工厂也将复制该模式。随着产品质量的提升,用户下线率也呈明显下降趋势。根据尤琼兵提供的数据,截至2017年10月,黄石东贝用户下线率较2014年下降63.64%。
除此之外,智能制造升级也提高了生产效率。据朱宇杉介绍,黄石东贝11条生产线最初产能为2700万台/年。在技术改造和智能化改造后,目前已达到3300万台/年。其中,变频压缩机标杆生产线可达到330万台/年。“2018年处,我们宿迁基地新生产线正式投产后,公司总产能将达到3600万台/年。除此之外,明年我们还将继续提高原有生产线的生产效率,最终产量有望达到3900万台/年。”
根据黄石东贝十三五规划,到2020年,在仅增加一条生产线的情况下,经过智能制造升级,黄石东贝产能将由2016年的3300万台/年增加到3900万台/年,其中变频产品产量将由300万台/年提高至1500万台/年,人均效率将由2016年3.2台/小时到2017年的5.2台/小时。
加速定制化生产模式
单品种、大批量是传统制造的特点。先生产再销售的模式,在一定程度上存在资源浪费。随着供给侧改革,更合理的生产模式是根据客户需求进行定制化生产。因此,多品种,小批量正成为发展趋势。“以前是我们做什么,卖给客户什么;现在是客户需要什么,我们做什么。这样更利于中国制造业成本降低,也更符合市场需求。资源利用率提高的同时,也会缩减库存。”而想要实现这种定制化生产,智能制造升级非常重要。
“传统的生产线增加一个品种,便需要开一个模具。生产线智能化升级后,只需要在设备数据库中修改相应的参数即可。”走到变频压缩机生产线的一道工序时,尤琼兵指着一台设备说,“比如这台弯管设备,操作人员只要输入相应的参数,就能实现产品角度变化。”据他介绍,这道工序生产的三根管子,是压缩机和冰箱连接的部分,分别为吸气管、排气管和制冷剂充注管。以前的生产线中,这3根管子的角度等都是标准化的。现在,冰箱企业也开始考虑产品结构、容量、压缩机位置等,对每根管子的角度都有了不同的角度需求。
“过去,我们只能依靠开模具来实现,但随着多品种、小批量趋势愈发突出,开模具成本越来越高。”尤琼兵进一步说道,“然后我们就在业内率先对这道工序进行了智能化升级,提高生产线柔性。以前我们需要超过100套模具,现在只需要一套设备即可完成。这道工序的自动化升级现在已经在全行业推广。”
值得一提的是,在尤琼兵看来,智能制造不是独立的,而是由上下游相互联通。就黄石东贝而言,智能制造是由整机企业向我们延伸。“比如客户会有一些个性化的需求,会通过网络向我们下单。我们在接到信息后,会将其发给研发部门,然后利用信息平台对制造系统进行指导。与此同时,我们也会向自己的上游进行辐射,把我们的需求告知供应商。最终实现真正的定制化。”
本文由 电器杂志 发表,转载请注明来源!